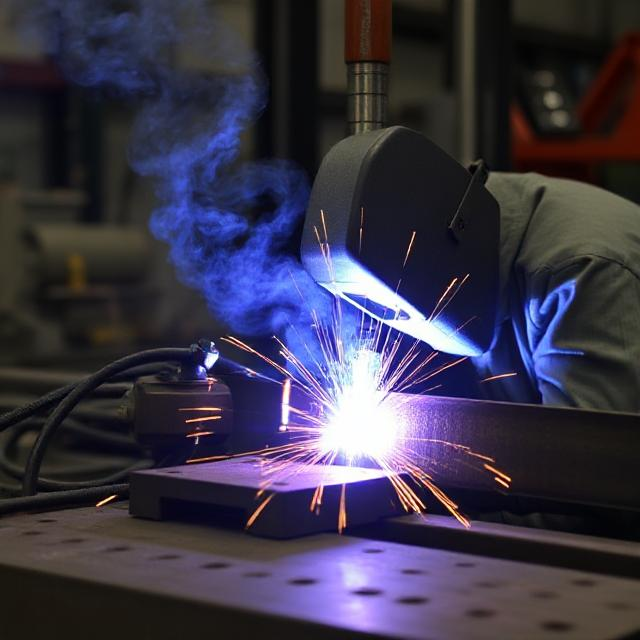
Electron Beam Welding (EBW)
1. Name of Process
- Electron Beam Welding (EBW).
2. Key Features
- Uses a high-velocity electron beam to generate heat and melt the metal.
- Performed in a vacuum to prevent electron scattering and contamination.
- Extremely precise with deep penetration and minimal heat-affected zones (HAZ).
- Suitable for high-strength and refractory materials.
3. Applications
- Aerospace (e.g., turbine blades, rocket components).
- Automotive (e.g., transmission parts, fuel injectors).
- Medical devices (e.g., implants, surgical tools).
- Electronics (e.g., hermetic sealing of components).
- Nuclear and energy industries (e.g., reactor components).
4. Recommended Tools and Equipment
- Electron beam welding machine.
- Vacuum chamber.
- High-voltage power supply.
- Electron gun with focusing lens.
- Fixtures for precise part alignment.
5. Setup and Settings
- Beam Current: Adjust based on material thickness and desired penetration.
- Accelerating Voltage: Typically ranges from 30 kV to 150 kV.
- Travel Speed: Optimize for consistent weld quality.
- Focus: Adjust the beam focus for precise control over weld depth and width.
6. Technique Tips
- Ensure precise alignment of parts using fixtures.
- Maintain a clean vacuum environment to avoid contamination.
- Use beam oscillation for wider welds or to control heat input.
- Perform trial runs on scrap material to fine-tune settings.
7. Common Challenges and Solutions
- Porosity: Ensure proper vacuum levels and clean base materials.
- Misalignment: Use precision fixtures and alignment tools.
- Excessive Penetration: Reduce beam current or increase travel speed.
- Beam Deflection: Shield the workpiece from magnetic fields.
8. Safety Considerations
- Wear protective gear to shield against X-rays generated during the process.
- Ensure the vacuum chamber is properly sealed and maintained.
- Follow strict safety protocols for high-voltage equipment.
- Train operators on handling electron beam equipment and vacuum systems.
Electron Beam Welding (EBW) FAQs
1. What is Electron Beam Welding (EBW)?
- Direct Response: EBW is a precision welding process that uses a high-velocity electron beam to melt and join materials, typically performed in a vacuum.
- Detailed Explanation: The electron beam is generated by accelerating electrons to high speeds using a high-voltage power supply. The beam is focused onto the workpiece, creating intense heat that melts the metal. The vacuum environment prevents contamination and ensures high-quality welds.
- Example: EBW is commonly used in aerospace to weld turbine blades, where precision and strength are critical.
2. What materials can be welded using EBW?
- Direct Response: EBW can weld a wide range of materials, including metals, alloys, and refractory materials.
- Detailed Explanation: Common materials include:
- Metals: Titanium, stainless steel, aluminum, copper.
- Alloys: Inconel, Hastelloy, tungsten alloys.
- Refractory Materials: Molybdenum, niobium, zirconium.
- Example: EBW is ideal for welding titanium components in medical implants due to its ability to produce clean, contamination-free welds.
3. What are the advantages of EBW?
- Direct Response: EBW offers deep penetration, minimal heat-affected zones (HAZ), and high precision.
- Detailed Explanation:
- Deep Penetration: Can weld thick materials in a single pass.
- Minimal HAZ: Reduces distortion and preserves material properties.
- High Precision: Suitable for complex geometries and small components.
- Example: In the automotive industry, EBW is used for fuel injectors, where precision and reliability are essential.
4. What are the limitations of EBW?
- Direct Response: EBW requires a vacuum, has high equipment costs, and is limited to specific joint designs.
- Detailed Explanation:
- Vacuum Requirement: Adds complexity and cost to the process.
- High Equipment Costs: EBW machines are expensive to purchase and maintain.
- Joint Design Limitations: Best suited for butt joints and limited to materials that can withstand vacuum conditions.
- Example: EBW is less suitable for large-scale production of simple components due to its high setup costs.
5. How does EBW compare to other welding processes?
- Direct Response: EBW offers superior precision and weld quality compared to processes like TIG or MIG but is more expensive and complex.
- Detailed Explanation:
- Precision: EBW produces narrower and deeper welds than TIG or MIG.
- Quality: The vacuum environment eliminates contamination, resulting in stronger welds.
- Cost: EBW is more expensive due to equipment and vacuum requirements.
- Example: In aerospace, EBW is preferred over TIG for critical components like rocket nozzles due to its superior weld integrity.
6. What safety precautions are needed for EBW?
- Direct Response: Safety measures include shielding against X-rays, proper vacuum chamber maintenance, and high-voltage equipment training.
- Detailed Explanation:
- X-Ray Shielding: Operators must wear protective gear and ensure the chamber is properly shielded.
- Vacuum Maintenance: Regularly check seals and pumps to prevent leaks.
- High-Voltage Safety: Follow strict protocols for handling and maintaining high-voltage equipment.
- Example: In nuclear applications, EBW operators undergo specialized training to handle radioactive materials safely.
7. What industries use EBW?
- Direct Response: EBW is used in aerospace, automotive, medical, electronics, and energy industries.
- Detailed Explanation:
- Aerospace: Turbine blades, rocket components.
- Automotive: Fuel injectors, transmission parts.
- Medical: Implants, surgical tools.
- Electronics: Hermetic sealing of sensors and components.
- Energy: Nuclear reactor components, heat exchangers.
- Example: EBW is used to weld fuel rods in nuclear reactors, where precision and reliability are critical.
8. Can EBW be automated?
- Direct Response: Yes, EBW can be automated for high-precision and repetitive tasks.
- Detailed Explanation: Automated EBW systems use CNC controls to precisely position the electron beam and workpiece. This is ideal for industries like aerospace and medical devices, where consistency is crucial.
- Example: Automated EBW is used to weld titanium alloy components for aircraft engines, ensuring consistent quality across thousands of parts.
9. What are the costs associated with EBW?
- Direct Response: EBW has high initial equipment costs and requires ongoing maintenance.
- Detailed Explanation:
- Equipment Costs: EBW machines can cost hundreds of thousands of dollars.
- Maintenance: Regular upkeep of the vacuum system and electron gun is required.
- Operational Costs: Energy consumption and skilled labor add to the expense.
- Example: A small aerospace manufacturer might invest in EBW for critical components but use cheaper processes for non-critical parts.
10. Where can I learn more about EBW?
-
-
- Direct Response: Resources include industry publications, training programs, and equipment manufacturers.
- Detailed Explanation:
- Publications: Journals like Welding Journal and Manufacturing Engineering.
- Training: Programs offered by organizations like the American Welding Society (AWS).
- Manufacturers: Companies like Sciaky and Pro-Beam provide detailed technical guides.
- Additional Resources:
-