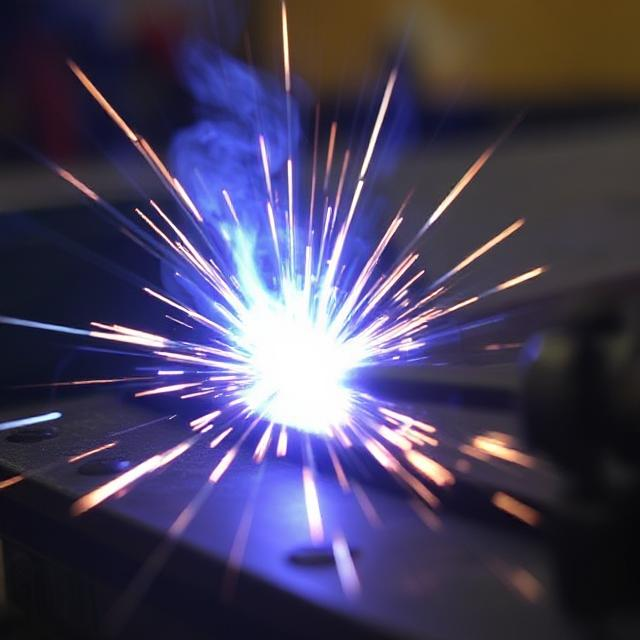
Name of Process:
Friction Stir Welding (FSW)
Key Features:
- A solid-state welding process that joins materials without melting them.
- Uses a rotating tool to generate frictional heat and mechanically mix materials.
- Produces high-strength, defect-free welds.
- Suitable for materials that are difficult to weld using traditional methods.
Applications:
- Aerospace (e.g., aircraft fuselages, fuel tanks).
- Automotive (e.g., lightweight aluminum components).
- Shipbuilding (e.g., hulls and decks).
- Railway and construction industries.
- Electronics (e.g., heat sinks and enclosures).
Recommended Tools and Equipment:
- FSW machine (manual or CNC-controlled).
- Rotating tool with a shoulder and pin (made of durable materials like tool steel).
- Clamping system to secure workpieces.
- Cooling system (if required for specific materials).
- Safety gear (gloves, goggles, and protective clothing).
Setup and Settings:
- Select the appropriate tool design and material for the workpiece.
- Secure the workpieces firmly to prevent movement during welding.
- Set the tool rotation speed, travel speed, and plunge depth based on material type and thickness.
- Calibrate the machine for consistent weld quality.
Technique Tips:
- Ensure proper alignment and fit-up of the workpieces.
- Use consistent tool rotation and travel speeds for uniform welds.
- Monitor tool wear and replace as needed to maintain weld quality.
- Optimize parameters (e.g., rotation speed, plunge depth) for specific materials.
Common Challenges and Solutions:
- Challenge: Tool wear or breakage.
Solution: Use high-quality tools and monitor wear regularly. - Challenge: Incomplete penetration or weak welds.
Solution: Adjust tool plunge depth and travel speed. - Challenge: Material distortion or cracking.
Solution: Optimize clamping and welding parameters.
Safety Considerations:
- Wear heat-resistant gloves, safety goggles, and protective clothing.
- Ensure proper ventilation to avoid inhaling fumes or dust.
- Regularly inspect equipment for wear or damage.
- Follow lockout/tagout procedures during maintenance.
- Keep a fire extinguisher nearby for emergencies.
1. What is Friction Stir Welding (FSW)?
Direct Response:
Friction Stir Welding (FSW) is a solid-state welding process that joins materials without melting them, using a rotating tool to generate frictional heat and mechanically mix the materials.
Detailed Explanation:
FSW involves a rotating tool with a shoulder and pin that plunges into the joint between two workpieces. The tool generates frictional heat, softening the material, and mechanically stirs it to create a strong, defect-free weld.
Example:
In aerospace manufacturing, FSW is used to join aluminum alloy panels for aircraft fuselages, ensuring lightweight and high-strength welds.
Additional Resources:
2. How does Friction Stir Welding work?
Direct Response:
FSW uses a rotating tool to generate frictional heat and mechanically mix materials, creating a solid-state weld without melting.
Detailed Explanation:
The tool rotates and moves along the joint line, generating heat through friction. The softened material is mechanically mixed by the tool’s pin, creating a strong bond as it cools.
Example:
A robotic FSW system might weld aluminum sheets for a ship’s hull, producing consistent, high-quality welds in minutes.
3. What materials can be welded using FSW?
Direct Response:
FSW is primarily used for welding aluminum, magnesium, and other non-ferrous metals, as well as some steels and composites.
Detailed Explanation:
FSW is ideal for materials that are difficult to weld using traditional methods, such as high-strength aluminum alloys. It can also weld dissimilar materials, like aluminum to steel.
Example:
A railway manufacturer might use FSW to join aluminum panels for lightweight train carriages.
4. What are the advantages of FSW?
Direct Response:
FSW offers high-strength welds, no melting, and the ability to weld difficult materials, making it ideal for aerospace, automotive, and shipbuilding.
Detailed Explanation:
FSW produces defect-free welds with minimal distortion, no filler materials, and excellent mechanical properties. It’s also environmentally friendly, as it doesn’t produce fumes or spatter.
Example:
In automotive manufacturing, FSW is used to join aluminum components, reducing vehicle weight and improving fuel efficiency.
5. What equipment is needed for FSW?
Direct Response:
Key equipment includes an FSW machine, rotating tools, a clamping system, and safety gear.
Detailed Explanation:
The FSW machine provides the rotational and translational motion, while the rotating tool (with a shoulder and pin) generates heat and mixes the material. A clamping system secures the workpieces, and safety gear protects the operator.
Example:
A shipbuilding company might use a large CNC-controlled FSW machine with water-cooled tools for welding aluminum hulls.
6. How do I set up and adjust an FSW machine?
Direct Response:
Set up involves selecting the right tool, securing the workpieces, and adjusting rotation speed, travel speed, and plunge depth.
Detailed Explanation:
Start by cleaning and aligning the workpieces. Choose a tool design suitable for the material and joint type. Set the machine parameters (e.g., 500–2000 RPM rotation speed, 50–500 mm/min travel speed) based on material thickness and type.
Example:
For welding 6mm aluminum sheets, you might set the rotation speed to 1000 RPM, travel speed to 200 mm/min, and plunge depth to 6.2mm.
7. What are common issues in FSW and how do I fix them?
Direct Response:
Common issues include tool wear, incomplete penetration, and material distortion, which can be fixed by adjusting parameters or maintaining equipment.
Detailed Explanation:
- Tool wear: Use high-quality tools and monitor wear regularly.
- Incomplete penetration: Increase plunge depth or reduce travel speed.
- Material distortion: Optimize clamping and welding parameters.
Example:
If welds are weak, increase the plunge depth or rotation speed slightly and test again.
8. What safety precautions should I take with FSW?
Direct Response:
Wear protective gear, ensure proper ventilation, and follow equipment maintenance protocols.
Detailed Explanation:
Protective gear includes heat-resistant gloves, safety goggles, and flame-resistant clothing. Ensure the workspace is well-ventilated to avoid inhaling dust or fumes, and regularly inspect equipment for wear or damage.
Example:
An operator should always wear gloves and goggles when using an FSW machine to protect against heat and moving parts.
9. Can FSW be automated?
Direct Response:
Yes, FSW can be automated using CNC-controlled or robotic systems for high-volume production.
Detailed Explanation:
Automated FSW systems are common in industries like aerospace and automotive, where precision and repeatability are critical. These systems use programmable machines to perform consistent, high-quality welds.
Example:
An aircraft manufacturer might use robotic FSW arms to weld aluminum panels for fuselages, ensuring consistent quality and reducing production time.
10. What industries use FSW?
Direct Response:
FSW is widely used in aerospace, automotive, shipbuilding, and railway industries.
Detailed Explanation:
FSW’s ability to produce high-strength, lightweight welds makes it ideal for industries requiring durable and efficient joining methods.
Example:
In shipbuilding, FSW is used to join aluminum panels for hulls and decks, reducing weight and improving fuel efficiency.