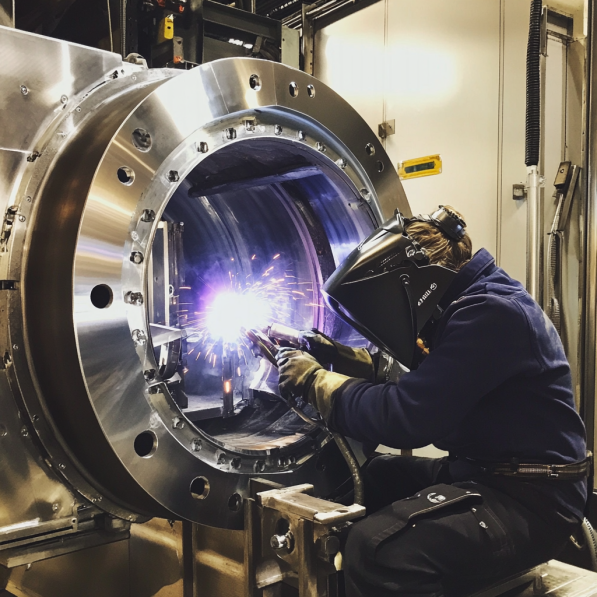
Name of Process
Gas Metal Arc Welding (GMAW), commonly known as “MIG Welding” (Metal Inert Gas).
Key Features
- Uses a continuous wire electrode fed through a welding gun.
- Requires shielding gas (e.g., argon, CO2, or a mix) to protect the weld pool.
- High welding speed and efficiency.
- Suitable for a wide range of metals, including steel, aluminum, and stainless steel.
- Easy to learn and ideal for beginners.
Applications
- Automotive repair and manufacturing.
- Fabrication of metal structures and equipment.
- DIY projects and home repairs.
- Industrial manufacturing and production lines.
Recommended Tools and Equipment
- MIG welding machine (with wire feed system).
- Shielding gas cylinder (argon, CO2, or mixed gas).
- Welding gun and consumable wire electrode.
- Welding helmet with auto-darkening lens.
- Gloves, apron, and protective clothing.
- Wire brush and grinder for cleaning.
Setup and Settings
- Choose the correct wire electrode and shielding gas for the material.
- Set the wire feed speed and voltage according to material thickness.
- Ensure proper gas flow rate (typically 20-25 CFH).
- Ground the workpiece securely.
- Adjust the welding gun nozzle and contact tip for optimal performance.
Technique Tips
- Maintain a consistent travel speed and gun angle (15-20 degrees).
- Use a push technique for better visibility and cleaner welds.
- Keep the wire electrode extension (stick-out) around 1/4 to 3/8 inch.
- Clean the workpiece thoroughly before welding.
Common Challenges and Solutions
- Porosity: Caused by inadequate shielding gas. Check gas flow and avoid drafts.
- Burn-Through: Prevent by reducing voltage or increasing travel speed on thin metals.
- Wire Feeding Issues: Clean the liner and ensure proper tension on the drive rolls.
- Spatter: Minimize by adjusting voltage and using anti-spatter spray.
Safety Considerations
- Wear proper PPE (helmet, gloves, flame-resistant clothing).
- Work in a well-ventilated area or use fume extraction to avoid inhaling harmful gases.
- Beware of electric shock; inspect cables and connections.
- Keep a fire extinguisher nearby and clear the work area of flammable materials.
1. What is MIG welding, and how does it work?
Direct Response:
MIG welding (Gas Metal Arc Welding or GMAW) is a process that uses a continuous wire electrode and shielding gas to create an electric arc, melting the metal and forming a weld.
Detailed Explanation:
The wire electrode is fed through a welding gun, and the shielding gas (e.g., argon, CO2) protects the weld pool from contamination. The arc melts the wire and the base metal, creating a strong bond.
Examples or Case Studies:
- Used in automotive manufacturing for body repairs.
- Commonly used in fabrication shops for building metal structures.
Additional Resources:
- Video tutorial: “How MIG Welding Works.”
- Article: “The Science Behind Gas Metal Arc Welding.”
2. What types of metals can be welded with MIG welding?
Direct Response:
MIG welding can weld steel, stainless steel, aluminum, and other non-ferrous metals.
Detailed Explanation:
- Steel: Use a solid wire electrode with CO2 or mixed gas.
- Stainless Steel: Use stainless steel wire with a tri-mix gas (argon, CO2, oxygen).
- Aluminum: Use aluminum wire with 100% argon gas.
Examples or Case Studies:
- Aluminum MIG welding is used in boat building and aerospace.
- Steel MIG welding is common in construction and automotive repair.
Additional Resources:
- Guide: “Choosing the Right Wire and Gas for MIG Welding.”
- Video: “MIG Welding Different Metals.”
3. What shielding gas should I use for MIG welding?
Direct Response:
The shielding gas depends on the material:
- Steel: CO2 or a mix of 75% argon and 25% CO2.
- Stainless Steel: Tri-mix gas (argon, CO2, oxygen).
- Aluminum: 100% argon.
Detailed Explanation:
Shielding gas prevents contamination and stabilizes the arc. Using the wrong gas can lead to poor weld quality.
Examples or Case Studies:
- A fabrication shop improved weld quality by switching to a 75/25 argon/CO2 mix for steel.
Additional Resources:
- Shielding gas selection chart.
- Article: “Understanding Shielding Gases for MIG Welding.”
4. How do I set the correct wire feed speed and voltage?
Direct Response:
Refer to the welding machine’s manual or a welding chart for recommended settings based on material thickness and wire diameter.
Detailed Explanation:
- Wire Feed Speed: Controls the amount of filler metal deposited.
- Voltage: Determines the heat input and arc stability.
Examples or Case Studies:
- A beginner achieved better welds after adjusting the wire feed speed to match the material thickness.
Additional Resources:
- Welding parameter chart.
- Video: “Setting Up Your MIG Welder.”
5. Can MIG welding be used outdoors?
Direct Response:
MIG welding can be used outdoors, but wind can disperse the shielding gas, leading to porosity. Use flux-cored wire for outdoor welding.
Detailed Explanation:
Flux-cored wire creates its own shielding, making it ideal for outdoor use.
Examples or Case Studies:
- Construction crews use flux-cored MIG welding for outdoor structural projects.
Additional Resources:
- Guide: “Outdoor Welding Tips for MIG Welding.”
- Video: “MIG Welding in the Field.”
6. What are the advantages of MIG welding over other methods?
Direct Response:
MIG welding is fast, easy to learn, and versatile, making it ideal for beginners and professionals.
Detailed Explanation:
- Speed: Continuous wire feed allows for faster welding.
- Ease of Use: Less skill required compared to TIG or stick welding.
- Versatility: Can weld a variety of metals and thicknesses.
Examples or Case Studies:
- MIG welding is the preferred method for automotive repair due to its speed and ease.
Additional Resources:
- Article: “MIG vs. TIG vs. Stick Welding: Which is Right for You?”
- Video: “Advantages of MIG Welding.”
7. How do I prevent porosity in MIG welds?
Direct Response:
Prevent porosity by ensuring proper gas flow, cleaning the workpiece, and avoiding drafts.
Detailed Explanation:
Porosity is caused by contaminants or inadequate shielding. Check gas hoses for leaks and clean the metal surface before welding.
Examples or Case Studies:
- A welder eliminated porosity by increasing the gas flow rate and cleaning the metal.
Additional Resources:
- Guide: “Common Weld Defects and How to Fix Them.”
- Video: “Preventing Porosity in MIG Welds.”
8. What safety gear is required for MIG welding?
Direct Response:
Essential safety gear includes a welding helmet, gloves, flame-resistant clothing, and safety boots.
Detailed Explanation:
- Helmet: Protects eyes from UV/IR radiation.
- Gloves: Insulate against heat and electric shock.
- Clothing: Prevents burns from sparks and molten metal.
- Boots: Protect feet from falling objects.
Examples or Case Studies:
- A welder avoided severe burns by wearing a flame-resistant jacket.
Additional Resources:
- Checklist: “Essential Welding Safety Gear.”
- Video: “Welding Safety Tips for Beginners.”
9. What are the most common mistakes beginners make with MIG welding?
Direct Response:
Common mistakes include incorrect settings, poor gun angle, and failing to clean the workpiece.
Detailed Explanation:
- Incorrect Settings: Leads to weak or inconsistent welds.
- Poor Gun Angle: Causes uneven bead appearance.
- Dirty Workpiece: Results in porosity and weak welds.
Examples or Case Studies:
- A beginner improved their welds significantly after learning to clean the metal properly.
Additional Resources:
- Guide: “Top 10 MIG Welding Mistakes and How to Avoid Them.”
- Video: “Beginner MIG Welding Tips.”
10. How do I troubleshoot wire feeding issues?
Direct Response:
Check for blockages in the liner, ensure proper tension on the drive rolls, and use the correct wire diameter.
Detailed Explanation:
Wire feeding issues can be caused by a dirty liner, incorrect drive roll tension, or using the wrong size wire.
Examples or Case Studies:
- A welder resolved feeding issues by cleaning the liner and adjusting the drive roll tension.
Additional Resources:
- Guide: “Troubleshooting MIG Welding Wire Feed Problems.”
- Video: “Fixing Wire Feeding Issues.”