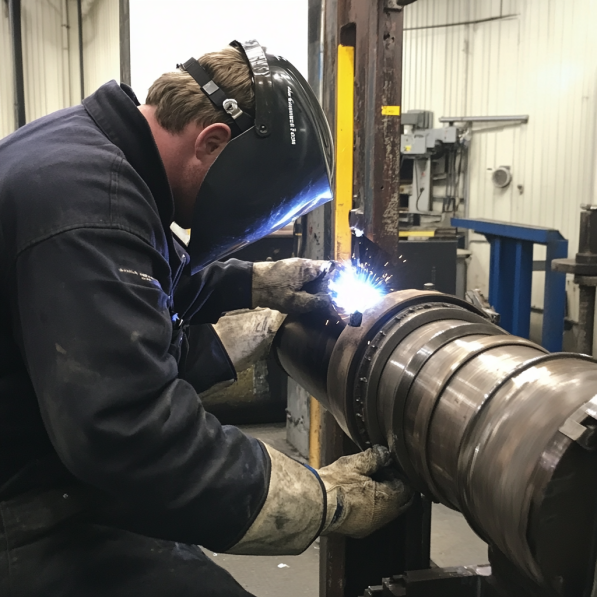
Name of Process
Gas Tungsten Arc Welding (GTAW), commonly known as “TIG Welding” (Tungsten Inert Gas).
Key Features
- Uses a non-consumable tungsten electrode to create the weld.
- Requires shielding gas (usually argon) to protect the weld pool.
- Produces high-quality, precise welds with excellent finish.
- Suitable for welding thin materials and a wide range of metals, including steel, aluminum, and stainless steel.
- Requires more skill and practice compared to other welding methods.
Applications
- Aerospace and aviation industries.
- Automotive repair and customization.
- Fabrication of high-precision components.
- Art and sculpture creation.
- Pipe and tube welding (e.g., in the food and beverage industry).
Recommended Tools and Equipment
- TIG welding machine (AC/DC capability for aluminum and steel).
- Tungsten electrodes (e.g., thoriated, ceriated, or lanthanated).
- Shielding gas cylinder (argon or argon/helium mix).
- TIG torch with collets and nozzles.
- Filler rods (matched to the base metal).
- Welding helmet with auto-darkening lens.
- Gloves, apron, and protective clothing.
- Wire brush and grinder for cleaning.
Setup and Settings
- Choose the correct tungsten electrode and grind it to the appropriate shape (pointed for DC, balled for AC).
- Select the right filler rod for the base metal.
- Set the machine to the correct polarity (DCEN for steel, AC for aluminum).
- Adjust amperage based on material thickness.
- Set the shielding gas flow rate (typically 15-20 CFH).
- Ensure proper grounding of the workpiece.
Technique Tips
- Maintain a consistent arc length (1/8 inch or less).
- Use a slight push or drag angle (10-15 degrees).
- Control the heat input by using a foot pedal or amperage control.
- Clean the workpiece thoroughly before welding.
- Practice steady hand movements for precise welds.
Common Challenges and Solutions
- Tungsten Contamination: Caused by touching the electrode to the workpiece. Regrind or replace the electrode.
- Porosity: Prevent by ensuring proper gas flow and cleaning the metal surface.
- Uneven Beads: Caused by inconsistent travel speed or arc length. Practice maintaining a steady hand.
- Cracking: Avoid by using the correct filler material and preheating thick materials.
Safety Considerations
- Wear proper PPE (helmet, gloves, flame-resistant clothing).
- Work in a well-ventilated area or use fume extraction to avoid inhaling harmful gases.
- Beware of electric shock; inspect cables and connections.
- Protect your eyes from UV/IR radiation with a proper welding helmet.
- Keep a fire extinguisher nearby and clear the work area of flammable materials.
1. What is TIG welding, and how does it work?
Direct Response:
TIG welding (Gas Tungsten Arc Welding or GTAW) uses a non-consumable tungsten electrode to create an electric arc, melting the metal and forming a weld. Shielding gas (usually argon) protects the weld pool from contamination.
Detailed Explanation:
The tungsten electrode generates the arc, and filler metal is added manually if needed. The shielding gas prevents oxidation and ensures a clean weld.
Examples or Case Studies:
- Used in aerospace for welding thin aluminum sheets.
- Commonly used in automotive customization for precision welds.
2. What types of metals can be welded with TIG welding?
Direct Response:
TIG welding can weld steel, stainless steel, aluminum, magnesium, copper, and other non-ferrous metals.
Detailed Explanation:
- Steel and Stainless Steel: Use DCEN (Direct Current Electrode Negative) polarity.
- Aluminum and Magnesium: Use AC (Alternating Current) polarity.
Examples or Case Studies:
- Aluminum TIG welding is used in bicycle frame fabrication.
- Stainless steel TIG welding is common in food processing equipment.
Additional Resources:
- Guide: “Choosing the Right Settings for TIG Welding Different Metals.”
- Video: “TIG Welding Aluminum vs. Steel.”
3. What shielding gas should I use for TIG welding?
Direct Response:
Argon is the most common shielding gas for TIG welding. For thicker materials, an argon/helium mix can be used.
Detailed Explanation:
Argon provides excellent arc stability and weld pool protection. Helium increases heat input, making it suitable for thicker materials.
Examples or Case Studies:
- A fabrication shop improved weld quality on thick aluminum by using a 75% argon/25% helium mix.
Additional Resources:
- Shielding gas selection chart.
- Article: “Understanding Shielding Gases for TIG Welding.”
4. How do I choose the right tungsten electrode?
Direct Response:
Choose the tungsten electrode based on the material and welding current:
- Thoriated (Red): For DC welding on steel.
- Ceriated (Gray): For AC/DC welding on aluminum and steel.
- Lanthanated (Gold): For general-purpose AC/DC welding.
Detailed Explanation:
The electrode type affects arc stability and performance. Always grind the electrode to the correct shape (pointed for DC, balled for AC).
Examples or Case Studies:
- A welder achieved better results on aluminum by switching to a ceriated electrode.
Additional Resources:
- Guide: “Selecting the Right Tungsten Electrode.”
- Video: “How to Grind Tungsten Electrodes for TIG Welding.”
5. Can TIG welding be used for thick materials?
Direct Response:
Yes, but it requires higher amperage, preheating, and multiple passes.
Detailed Explanation:
TIG welding is better suited for thin to medium-thickness materials. For thick materials, consider using a multi-pass technique or switching to a more efficient method like MIG welding.
Examples or Case Studies:
- A shipyard used TIG welding for thick stainless steel pipes by preheating and using multiple passes.
Additional Resources:
- Guide: “Welding Thick Materials with TIG.”
- Video: “TIG Welding Thick vs. Thin Metal.”
6. What are the advantages of TIG welding over other methods?
Direct Response:
TIG welding produces high-quality, precise welds with excellent finish and no spatter.
Detailed Explanation:
- Precision: Ideal for thin materials and detailed work.
- Versatility: Can weld a wide range of metals.
- Cleanliness: No slag or spatter to clean up.
Examples or Case Studies:
- TIG welding is preferred for artistic metalwork due to its precision.
Additional Resources:
- Article: “TIG vs. MIG vs. Stick Welding: Which is Right for You?”
- Video: “Advantages of TIG Welding.”
7. How do I prevent tungsten contamination?
Direct Response:
Avoid touching the tungsten electrode to the workpiece or filler rod.
Detailed Explanation:
Tungsten contamination occurs when the electrode touches the weld pool, causing it to degrade. Maintain a consistent arc length and use proper technique.
Examples or Case Studies:
- A beginner improved their welds by practicing arc length control.
Additional Resources:
- Guide: “Common TIG Welding Mistakes and How to Fix Them.”
- Video: “Preventing Tungsten Contamination.”
8. What safety gear is required for TIG welding?
Direct Response:
Essential safety gear includes a welding helmet, gloves, flame-resistant clothing, and safety boots.
Detailed Explanation:
- Helmet: Protects eyes from UV/IR radiation.
- Gloves: Insulate against heat and electric shock.
- Clothing: Prevents burns from sparks and molten metal.
- Boots: Protect feet from falling objects.
Examples or Case Studies:
- A welder avoided severe burns by wearing a flame-resistant jacket.
Additional Resources:
- Checklist: “Essential Welding Safety Gear.”
- Video: “Welding Safety Tips for Beginners.”
9. What are the most common mistakes beginners make with TIG welding?
Direct Response:
Common mistakes include incorrect arc length, poor filler rod control, and inadequate gas coverage.
Detailed Explanation:
- Incorrect Arc Length: Causes inconsistent welds.
- Poor Filler Rod Control: Leads to uneven bead appearance.
- Inadequate Gas Coverage: Results in porosity.
Examples or Case Studies:
- A beginner improved their welds significantly after learning proper gas flow settings.
Additional Resources:
- Guide: “Top 10 TIG Welding Mistakes and How to Avoid Them.”
- Video: “Beginner TIG Welding Tips.”
10. How do I troubleshoot arc instability?
Direct Response:
Check for proper gas flow, clean the tungsten electrode, and ensure correct polarity settings.
Detailed Explanation:
Arc instability can be caused by contaminated tungsten, incorrect gas flow, or improper machine settings.
Examples or Case Studies:
- A welder resolved arc instability by cleaning the tungsten electrode and adjusting the gas flow rate.
Additional Resources:
-
- Guide: “Troubleshooting TIG Welding Arc Instability.”
- Video: “Fixing Arc Instability in TIG Welding.”