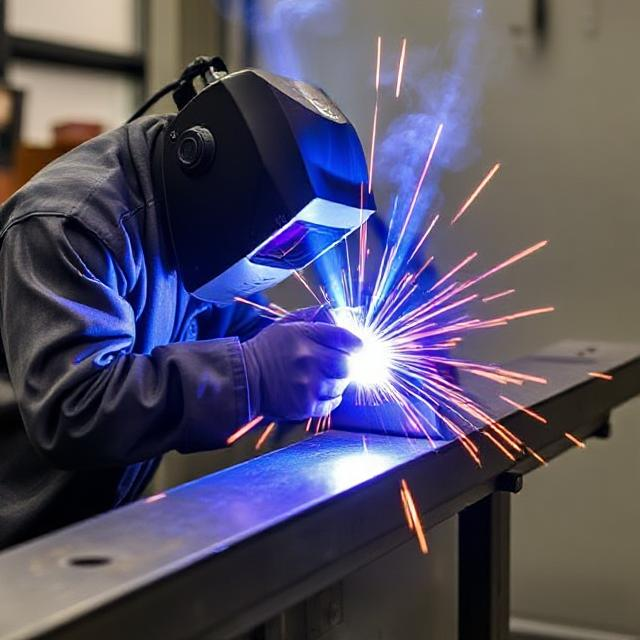
1. Name of Process:
Laser Beam Welding (LBW)
2. Key Features:
- High precision and accuracy
- Deep penetration with minimal heat-affected zone (HAZ)
- Fast welding speeds
- Suitable for thin and thick materials
- Non-contact process, reducing contamination
3. Applications:
- Automotive and aerospace industries
- Medical device manufacturing
- Electronics and micro-welding
- Jewelry and precision tooling
- Joining dissimilar metals
4. Recommended Tools and Equipment:
- High-power laser source (CO2, Nd:YAG , or fiber lasers)
- Beam delivery system (mirrors or fiber optics)
- CNC or robotic positioning system
- Shielding gas (argon, helium, or nitrogen)
- Cooling system for laser and workpiece
5. Setup and Settings:
- Align laser beam with joint seam
- Set appropriate power, speed, and focal length
- Choose shielding gas and flow rate
- Calibrate CNC or robotic system for precise movement
6. Technique Tips:
- Maintain consistent beam focus on the workpiece
- Use pulse welding for thin materials to avoid burn-through
- Optimize travel speed to balance penetration and weld quality
- Ensure proper joint fit-up and cleanliness
7. Common Challenges and Solutions:
- Porosity: Use proper shielding gas and clean workpiece surfaces.
- Cracking: Preheat materials or use filler metals for sensitive alloys.
- Inconsistent penetration: Adjust beam focus and power settings.
- Reflectivity issues: Use anti-reflective coatings or higher power lasers for reflective materials.
8. Safety Considerations:
- Wear laser safety goggles to protect eyes from beam exposure.
- Use enclosures or barriers to contain laser radiation.
- Ensure proper ventilation to avoid fumes and particulates.
- Follow manufacturer guidelines for laser operation and maintenance.
- Train personnel on laser safety protocols and emergency procedures.
Laser Beam Welding FAQ
1. What is Laser Beam Welding (LBW)?
Direct Response:
Laser Beam Welding (LBW) is a high-precision welding process that uses a focused laser beam to join materials, typically metals, with minimal heat-affected zones and high accuracy.
Detailed Explanation:
LBW works by directing a concentrated laser beam onto the workpiece, melting the material at the joint to form a weld. The process is highly controllable, allowing for deep penetration and narrow welds, making it ideal for applications requiring precision.
Examples or Case Studies:
- Used in the automotive industry to weld transmission components with high strength and precision.
- Applied in medical device manufacturing to join tiny, intricate parts without damaging surrounding areas.
Additional Resources:
- Laser Welding Basics – American Welding Society (AWS)
- Laser Beam Welding Applications – ScienceDirect
2. What materials can be welded using LBW?
Direct Response:
LBW can weld a wide range of materials, including stainless steel, aluminum, titanium, copper, and even dissimilar metals.
Detailed Explanation:
The process is versatile due to the laser’s ability to focus intense heat on a small area, making it suitable for both reflective and non-reflective materials. However, highly reflective materials like copper may require specialized lasers or surface treatments.
Examples or Case Studies:
- Aluminum alloys welded for aerospace components.
- Dissimilar metals like steel and titanium joined for medical implants.
Additional Resources:
3. What are the advantages of LBW over traditional welding methods?
Direct Response:
LBW offers higher precision, faster welding speeds, deeper penetration, and minimal heat-affected zones compared to traditional methods like TIG or MIG welding.
Detailed Explanation:
The focused laser beam allows for precise control over the weld, reducing distortion and enabling welding of thin or delicate materials. It also eliminates the need for filler material in many cases.
Examples or Case Studies:
- Automotive manufacturers use LBW to reduce production time and improve weld quality.
- Electronics industry benefits from LBW’s ability to weld small components without damaging nearby parts.
Additional Resources:
4. What are the limitations of LBW?
Direct Response:
LBW has high equipment costs, requires skilled operators, and can struggle with highly reflective materials.
Detailed Explanation:
The initial investment in laser equipment and setup can be significant. Additionally, reflective materials like copper and aluminum may require higher power lasers or surface treatments to achieve consistent results.
Examples or Case Studies:
- Small-scale manufacturers may find LBW cost-prohibitive compared to traditional methods.
- Reflective materials often require specialized fiber lasers for effective welding.
Additional Resources:
5. How do I choose the right laser for LBW?
Direct Response:
The choice of laser depends on the material, thickness, and application. Common options include CO2, Nd:YAG , and fiber lasers.
Detailed Explanation:
- CO2 Lasers: Best for thick materials and deep penetration.
- Nd:YAG Lasers: Suitable for precision welding of thin materials.
- Fiber Lasers: Ideal for reflective materials and high-speed applications.
Examples or Case Studies:
- Fiber lasers are widely used in the automotive industry for welding aluminum components.
- Nd:YAG lasers are preferred for medical device manufacturing due to their precision.
Additional Resources:
6. What safety precautions are necessary for LBW?
Direct Response:
Safety precautions include wearing laser safety goggles, using enclosures, ensuring proper ventilation, and following manufacturer guidelines.
Detailed Explanation:
Laser beams can cause severe eye and skin damage, so protective gear and barriers are essential. Proper ventilation is also critical to avoid inhaling fumes or particulates generated during welding.
Examples or Case Studies:
- Industrial facilities use enclosed laser systems with interlock mechanisms to prevent accidental exposure.
- Operators are trained in emergency shutdown procedures and first aid for laser-related injuries.
Additional Resources: