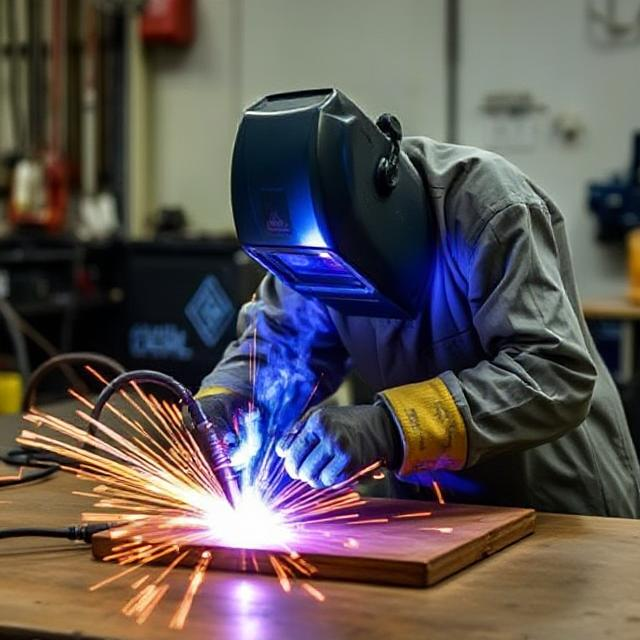
-
- Name of Process: Oxy-Acetylene Welding (OAW)
- Key Features:
- Uses a flame produced by burning acetylene gas with oxygen.
- Versatile process for welding, cutting, brazing, and heating.
- Portable and does not require electricity.
- Suitable for thin materials and repair work.
- Provides precise control over heat input.
- Applications:
- Repair and maintenance of automotive parts.
- Metal fabrication and sculpture.
- HVAC (heating, ventilation, and air conditioning) systems.
- Plumbing and pipefitting.
- Jewelry making and small-scale metalwork.
- Recommended Tools and Equipment:
- Oxygen and acetylene cylinders with regulators.
- Welding torch with interchangeable tips.
- Hoses and check valves for gas flow.
- Filler rods (appropriate for the base metal).
- Spark lighter and welding goggles.
- Setup and Settings:
- Secure oxygen and acetylene cylinders upright and chain them in place.
- Attach regulators and hoses, ensuring no leaks.
- Set oxygen pressure to 10-15 psi and acetylene pressure to 5-7 psi (adjust based on torch size and material thickness).
- Use a neutral flame (equal parts oxygen and acetylene) for most welding tasks.
- Technique Tips:
- Maintain a consistent torch angle (45° to 60°) and distance from the workpiece.
- Use a back-and-forth or circular motion to evenly distribute heat.
- Add filler rod to the leading edge of the weld pool for smooth, uniform welds.
- Practice controlling the flame and heat input on scrap material before welding the final piece.
- Common Challenges and Solutions:
- Porosity: Clean the base metal thoroughly and use the correct flame type.
- Burn-Through: Reduce heat input by increasing travel speed or using a smaller tip.
- Incomplete Fusion: Ensure proper flame adjustment and preheat thicker materials.
- Flame Instability: Check for leaks, proper gas pressures, and clean torch tips.
- Safety Considerations:
- Wear appropriate PPE (welding goggles, gloves, flame-resistant clothing).
- Ensure proper ventilation to avoid inhaling fumes.
- Store gas cylinders in a secure, upright position away from heat sources.
- Use flashback arrestors to prevent flame from traveling into the hoses.
- Keep a fire extinguisher nearby and inspect equipment regularly for leaks or damage.
1. What is Oxy-Acetylene Welding (OAW)?
Direct Response: Oxy-Acetylene Welding (OAW) is a gas welding process that uses a flame produced by burning acetylene gas with oxygen to join metals, primarily for thin materials and repair work.
Detailed Explanation: OAW involves mixing oxygen and acetylene in a welding torch to create a high-temperature flame (up to 3,500°C or 6,332°F). The flame melts the base metal and filler rod, forming a weld pool that solidifies into a strong joint. It is a versatile process used for welding, cutting, brazing, and heating.
Example: OAW is commonly used in automotive repair to weld thin sheet metal or exhaust systems.
Additional Resources: American Welding Society (AWS) Guide to OAW
2. What materials can be welded using OAW?
Direct Response: OAW is suitable for welding mild steel, stainless steel, cast iron, and some non-ferrous metals like copper and brass.
Detailed Explanation: OAW is ideal for thin materials (up to 6mm thick) and is often used for repair work or small-scale fabrication. It is not typically used for aluminum or magnesium due to their high thermal conductivity and melting points.
Example: In plumbing, OAW is used to weld copper pipes for water and gas lines.
Additional Resources: Material Compatibility Chart for OAW
3. What are the advantages of OAW over other welding processes?
Direct Response: OAW is portable, versatile, and does not require electricity, making it ideal for fieldwork and repairs.
Detailed Explanation: Unlike electric welding processes, OAW uses gas cylinders, making it suitable for remote locations. It can weld, cut, braze, and heat metals, offering flexibility for various tasks. Additionally, it provides precise control over heat input, reducing the risk of warping thin materials.
Example: In HVAC systems, OAW is used to braze copper tubing for refrigeration lines.
4. What are the common challenges in OAW and how can they be addressed?
Direct Response: Common challenges include porosity, burn-through, and flame instability, which can be mitigated through proper setup and technique.
Detailed Explanation:
- Porosity: Clean the base metal thoroughly and use the correct flame type (neutral flame).
- Burn-Through: Reduce heat input by increasing travel speed or using a smaller torch tip.
- Flame Instability: Check for leaks, ensure proper gas pressures, and clean torch tips.
- Incomplete Fusion: Preheat thicker materials and adjust the flame for better penetration.
Example: In automotive repair, using a smaller torch tip and faster travel speed prevents burn-through on thin sheet metal.
5. What safety precautions should be taken during OAW?
Direct Response: Wear appropriate PPE, ensure proper ventilation, and follow gas cylinder safety protocols to prevent accidents.
Detailed Explanation:
- PPE: Use welding goggles with a shade 5 lens, gloves, and flame-resistant clothing.
- Ventilation: Work in a well-ventilated area or use exhaust systems to avoid inhaling fumes.
- Gas Cylinders: Store cylinders upright, secure them with chains, and keep them away from heat sources.
- Fire Safety: Keep a fire extinguisher nearby and inspect equipment for leaks.
- Flashback Arrestors: Install them on hoses to prevent flames from traveling back into the cylinders.
Example: In fieldwork, flashback arrestors are essential to prevent accidents when moving the torch and hoses.
Additional Resources: OSHA Welding Safety Guidelines
6. Can OAW be used for cutting metals?
Direct Response: Yes, OAW can be used for cutting metals by adjusting the torch to create an oxidizing flame.
Detailed Explanation: The oxy-acetylene cutting process uses a high-temperature flame to preheat the metal, while a stream of pure oxygen oxidizes and blows away the molten metal. This method is effective for cutting mild steel and other ferrous metals.
Example: In scrap metal recycling, OAW is used to cut large steel beams into smaller pieces.
Additional Resources: Guide to Oxy-Acetylene Cutting
7. What equipment is needed for OAW?
Direct Response: Key equipment includes oxygen and acetylene cylinders, regulators, a welding torch, hoses, filler rods, and safety gear.
Detailed Explanation:
- Cylinders: Store oxygen and acetylene gases under pressure.
- Regulators: Control gas flow and pressure to the torch.
- Welding Torch: Mixes gases and directs the flame.
- Hoses: Transport gases from cylinders to the torch.
- Filler Rods: Add material to the weld pool for stronger joints.
- Safety Gear: Includes goggles, gloves, and flame-resistant clothing.
Example: In metal sculpture, artists use portable OAW kits to create intricate designs.
Additional Resources: OAW Equipment Buying Guide