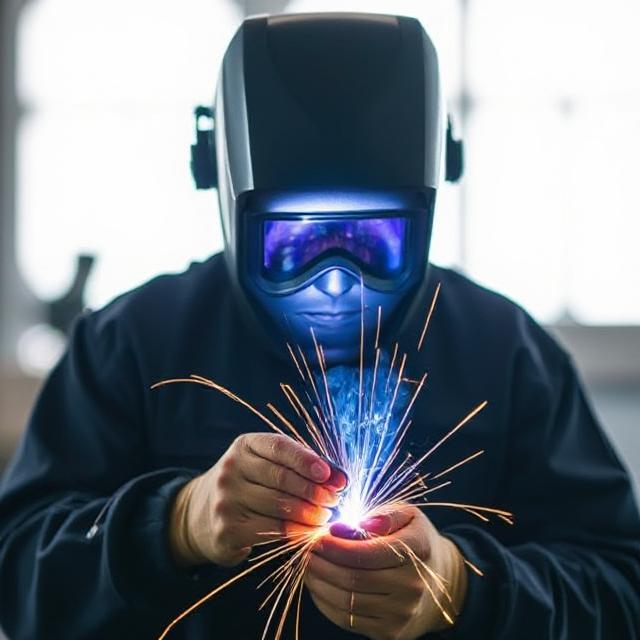
- Name of Process: Plasma Arc Welding (PAW)
- Key Features:
- Uses a concentrated plasma arc for high precision and control.
- Capable of welding thin materials and intricate joints.
- Produces clean, high-quality welds with minimal distortion.
- Operates in two modes: transferred arc (for conductive materials) and non-transferred arc (for non-conductive materials).
- Offers deeper penetration than TIG welding at similar amperages.
- Applications:
- Aerospace and aviation components.
- Medical device manufacturing.
- Precision welding of thin sheets and tubes.
- Automotive and electronics industries.
- Repair and maintenance of high-value components.
- Recommended Tools and Equipment:
- PAW power source with high-frequency start.
- Plasma torch with consumables (electrode, nozzle, shield cap).
- Gas supply (argon, argon-hydrogen mix, or helium).
- Cooling system (water or air-cooled torch).
- Fixturing and alignment tools for precision work.
- Setup and Settings:
- Select appropriate gas mixture based on material and application.
- Set amperage, gas flow rate, and travel speed for the desired weld profile.
- Ensure proper alignment of the torch and workpiece.
- Use a pilot arc to stabilize the plasma arc before welding.
- Technique Tips:
- Maintain a consistent torch angle and travel speed.
- Use a filler rod if required for thicker materials or specific joint types.
- Keep the nozzle clean to avoid arc instability.
- Practice on scrap material to fine-tune settings before welding the final piece.
- Common Challenges and Solutions:
- Arc Instability: Check gas flow rate and nozzle condition.
- Porosity: Ensure proper gas shielding and clean base metal.
- Excessive Heat Input: Adjust amperage and travel speed to avoid warping.
- Nozzle Damage: Replace consumables regularly and avoid contact with the workpiece.
- Safety Considerations:
- Wear appropriate PPE (helmet with shade 9-12, gloves, flame-resistant clothing).
- Ensure proper ventilation to avoid inhaling fumes.
- Protect eyes and skin from intense UV radiation.
- Follow electrical safety protocols to prevent shocks.
- Handle hot materials and equipment with care to avoid burns.
FAQ Content: Plasma Arc Welding (PAW)
1. What is Plasma Arc Welding (PAW)?
Direct Response: Plasma Arc Welding (PAW) is a precision welding process that uses a concentrated plasma arc to join materials, offering high control and quality for thin or intricate welds.
Detailed Explanation: PAW generates a plasma arc by ionizing gas (usually argon or argon-hydrogen mixtures) within a torch, creating a high-temperature, high-energy arc. This process is similar to TIG welding but provides greater arc stability, deeper penetration, and better control over the weld pool. It operates in two modes: transferred arc (for conductive materials) and non-transferred arc (for non-conductive materials).
Example: PAW is used in aerospace manufacturing to weld thin titanium sheets for aircraft components, ensuring precision and strength.
Additional Resources: American Welding Society (AWS) Guide to PAW
2. What materials can be welded using PAW?
Direct Response: PAW is suitable for welding stainless steel, titanium, nickel alloys, and other high-performance metals, as well as thin sheets and precision components.
Detailed Explanation: PAW excels with materials that require high precision and minimal heat distortion, such as those used in aerospace, medical devices, and electronics. It is not typically used for aluminum or copper due to their high thermal conductivity, which can make the process less efficient.
Example: In medical device manufacturing, PAW is used to weld stainless steel surgical instruments with minimal heat-affected zones.
Additional Resources: Material Compatibility Chart for PAW
3. What are the advantages of PAW over TIG welding?
Direct Response: PAW offers greater arc stability, deeper penetration, and better control over the weld pool, making it ideal for precision applications.
Detailed Explanation: Compared to TIG welding, PAW produces a more focused and stable arc, allowing for higher energy density and faster travel speeds. This results in less distortion, especially in thin materials, and the ability to weld in keyhole mode for full penetration in thicker materials.
Example: In automotive manufacturing, PAW is used to weld exhaust systems with precision and minimal heat input, reducing warping.
4. What are the common challenges in PAW and how can they be addressed?
Direct Response: Common challenges include arc instability, porosity, and nozzle damage, which can be mitigated through proper setup and maintenance.
Detailed Explanation:
- Arc Instability: Ensure proper gas flow rates and replace worn consumables.
- Porosity: Clean the base metal thoroughly and use high-purity shielding gases.
- Nozzle Damage: Regularly inspect and replace the nozzle to maintain arc focus.
- Excessive Heat Input: Adjust amperage and travel speed to avoid warping.
Example: In electronics manufacturing, maintaining a clean work environment and using high-purity argon prevents contamination and porosity in delicate welds.
5. What safety precautions should be taken during PAW?
Direct Response: Wear appropriate PPE, ensure proper ventilation, and follow electrical safety protocols to protect against UV radiation, fumes, and burns.
Detailed Explanation:
- PPE: Use a welding helmet with a shade 9-12 lens, gloves, and flame-resistant clothing.
- Ventilation: Ensure adequate airflow to avoid inhaling fumes generated during welding.
- Electrical Safety: Inspect equipment for damaged cables and ensure proper grounding.
- UV Radiation: Protect eyes and skin from the intense UV light produced by the plasma arc.
Example: In industrial settings, welding curtains and exhaust systems are used to protect workers from UV radiation and fumes.
Additional Resources: OSHA Welding Safety Guidelines
6. Can PAW be automated?
Direct Response: Yes, PAW can be automated for high-precision applications, such as in aerospace and medical device manufacturing.
Detailed Explanation: Automated PAW systems use robotic arms and CNC controls to achieve consistent, high-quality welds. This is particularly useful for repetitive tasks or complex geometries that require extreme precision.
Example: In the aerospace industry, automated PAW systems weld turbine blades with consistent accuracy, ensuring compliance with strict quality standards.
Additional Resources: Automated Welding Systems Guide
7. What equipment is needed for PAW?
Direct Response: Key equipment includes a PAW power source, plasma torch, gas supply, cooling system, and fixturing tools.
Detailed Explanation:
- Power Source: Provides the necessary current and high-frequency start.
- Plasma Torch: Holds consumables (electrode, nozzle, shield cap) and directs the plasma arc.
- Gas Supply: Typically argon or argon-hydrogen mixtures for shielding and plasma generation.
- Cooling System: Water or air-cooled torches to prevent overheating.
- Fixturing Tools: Secure the workpiece for precise alignment.
Example: In precision manufacturing, water-cooled torches are used to maintain consistent performance during long welding sessions.
Additional Resources: PAW Equipment Buying Guide