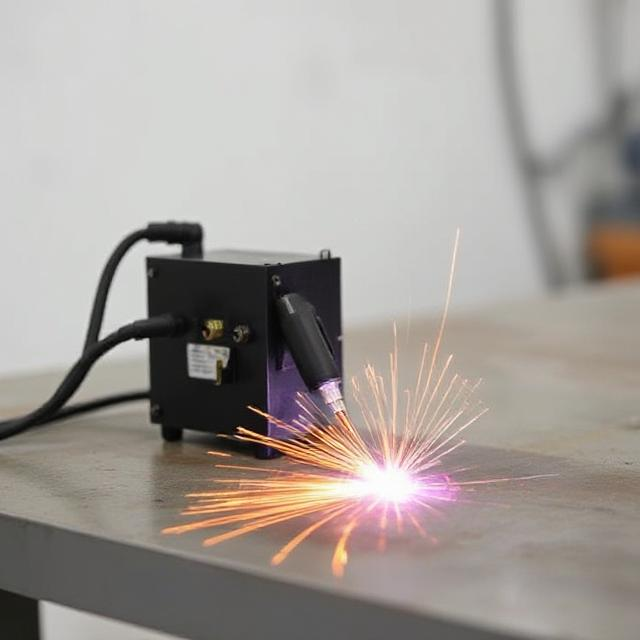
Name of Process:
Resistance Spot Welding (RSW)
Key Features:
- A welding process that joins metal surfaces by applying heat and pressure at specific points.
- Uses electrical resistance to generate heat at the weld point.
- Fast, efficient, and suitable for high-volume production.
- Produces strong, localized welds without filler material.
Applications:
- Automotive industry (e.g., car body assembly).
- Electronics (e.g., battery packs, circuit boards).
- Aerospace and appliance manufacturing.
- Sheet metal fabrication.
Recommended Tools and Equipment:
- Resistance spot welding machine (manual or automated).
- Electrodes (copper alloy tips for conductivity and durability).
- Cooling system (water or air) to prevent overheating.
- Foot pedal or robotic controls for precision.
- Safety gear (gloves, goggles, and protective clothing).
Setup and Settings:
- Choose the appropriate electrode shape and size for the material.
- Set the welding current, time, and pressure based on material thickness and type.
- Ensure proper alignment of the workpieces.
- Calibrate the machine for consistent weld quality.
Technique Tips:
- Clean the metal surfaces to remove contaminants (e.g., oil, rust).
- Apply consistent pressure to ensure proper contact between electrodes and workpieces.
- Use the shortest welding time necessary to avoid overheating.
- Monitor weld quality (e.g., nugget size, penetration) regularly.
Common Challenges and Solutions:
- Challenge: Inconsistent weld quality.
Solution: Check electrode alignment, pressure, and current settings. - Challenge: Electrode wear or sticking.
Solution: Use high-quality electrodes and maintain proper cooling. - Challenge: Burn-through or weak welds.
Solution: Adjust current and welding time for material thickness.
Safety Considerations:
- Wear heat-resistant gloves, safety goggles, and protective clothing.
- Ensure proper ventilation to avoid inhaling fumes.
- Regularly inspect equipment for wear or damage.
- Follow lockout/tagout procedures during maintenance.
- Keep a fire extinguisher nearby for emergencies.
-
1. What is Resistance Spot Welding (RSW)?
Resistance Spot Welding (RSW) is a process that joins metal surfaces by applying heat and pressure at specific points using electrical resistance.
RSW works by passing an electric current through two or more metal sheets held together by electrodes. The resistance to the current generates heat, melting the metal at the contact points. Pressure from the electrodes fuses the materials together, creating a strong weld nugget.
Example:
In automotive manufacturing, RSW is used to join sheet metal panels for car bodies, ensuring strong, consistent welds without the need for additional materials.Additional Resources:
- American Welding Society (AWS) Guide to RSW
- Miller Welding’s article on RSW basics
2. How does Resistance Spot Welding work?
RSW uses electrical resistance to generate heat at the weld point, melting the metal, while pressure from electrodes fuses the materials together.
When the electrodes press the metal sheets together and an electric current passes through, the resistance at the contact points creates heat. This heat melts the metal, forming a weld nugget as it cools. The process is quick, typically taking less than a second per weld.
Example:
A robotic RSW system in a factory might weld 50 spots on a car door in under a minute, ensuring high productivity and consistent quality.
3. What materials can be welded using RSW?
RSW is primarily used for welding low-resistance metals like steel, stainless steel, and aluminum.
RSW works best with conductive metals that have low electrical resistance. Steel and stainless steel are commonly welded, while aluminum requires specialized equipment due to its higher conductivity and lower melting point.
Example:
A kitchen appliance manufacturer might use RSW to join stainless steel panels for ovens or refrigerators.
4. What are the advantages of RSW?
RSW offers fast welding speeds, strong welds, and no need for filler materials, making it ideal for high-volume production.
RSW is highly efficient, producing consistent welds in seconds. It’s cost-effective for mass production and creates clean, localized welds without additional materials.
Example:
In the automotive industry, RSW allows for the rapid assembly of car bodies, reducing production time and costs.
5. What equipment is needed for RSW?
Key equipment includes a resistance spot welding machine, electrodes, a cooling system, and safety gear.
The welding machine provides the current and pressure, while electrodes (usually copper alloy) conduct the current and apply pressure. A cooling system prevents overheating, and safety gear protects the operator.
Example:
A small workshop might use a benchtop RSW machine with water-cooled electrodes for precision work.
6. How do I set up and adjust an RSW machine?
Direct Response:
Set up involves selecting the right electrodes, adjusting current, pressure, and welding time based on material thickness and type.Detailed Explanation:
Start by cleaning the metal surfaces and aligning the electrodes. Adjust the machine settings (current, time, pressure) according to the material specifications. Test the settings on scrap material before welding the final piece.Example:
For welding 1mm steel sheets, you might set the current to 8,000 amps, welding time to 0.2 seconds, and electrode pressure to 200 psi.
7. What are common issues in RSW and how do I fix them?
Direct Response:
Common issues include inconsistent welds, electrode wear, and burn-through, which can be fixed by adjusting settings or maintaining equipment.Detailed Explanation:
- Inconsistent welds: Check electrode alignment and pressure.
- Electrode wear: Replace or dress electrodes regularly.
- Burn-through: Reduce current or welding time.
Example:
If welds are weak, increase the pressure or current slightly and test again.
8. What safety precautions should I take with RSW?
Direct Response:
Wear protective gear, ensure proper ventilation, and follow equipment maintenance protocols.Detailed Explanation:
Protective gear includes heat-resistant gloves, safety goggles, and flame-resistant clothing. Ensure the workspace is well-ventilated to avoid inhaling fumes, and regularly inspect equipment for wear or damage.Example:
A welder should always wear gloves and goggles when operating an RSW machine to protect against sparks and heat.
9. Can RSW be automated?
Direct Response:
Yes, RSW can be automated using robotic systems for high-volume production.Detailed Explanation:
Robotic RSW systems are common in industries like automotive manufacturing, where precision and speed are critical. These systems use programmable robots to perform consistent, high-quality welds.Example:
A car manufacturer might use robotic RSW arms to weld hundreds of spots on a vehicle chassis in minutes.
10. What industries use RSW?
Direct Response:
RSW is widely used in automotive, aerospace, electronics, and appliance manufacturing.Detailed Explanation:
RSW’s speed, efficiency, and ability to produce strong welds make it ideal for industries requiring high-volume production and precision.Example:
In electronics, RSW is used to assemble battery packs for devices like smartphones and laptops.