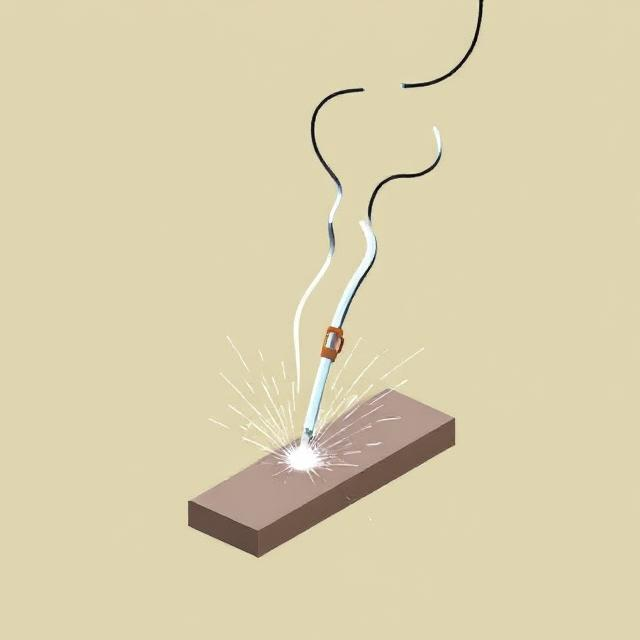
- Name of Process: Submerged Arc Welding (SAW)
- Key Features:
- High deposition rates and deep weld penetration.
- Automated or semi-automated process.
- Uses a granular flux to shield the arc and molten weld pool.
- Suitable for thick materials and long, continuous welds.
- Produces high-quality, clean welds with minimal spatter.
- Applications:
- Heavy fabrication (e.g., pressure vessels, shipbuilding).
- Structural steelwork (e.g., bridges, pipelines).
- Railroad construction and repair.
- Thick plate welding in industrial manufacturing.
- Recommended Tools and Equipment:
- SAW power source (constant voltage or constant current).
- Wire feeder and welding head.
- Flux hopper and recovery system.
- Welding torch or gun.
- Ground clamp and workpiece fixtures.
- Setup and Settings:
- Choose appropriate wire diameter and flux type for the material.
- Set voltage, amperage, and travel speed based on material thickness.
- Ensure proper alignment of the welding head and workpiece.
- Preheat thick materials if necessary.
- Technique Tips:
- Maintain consistent travel speed for uniform weld beads.
- Adjust flux depth to ensure proper coverage and arc stability.
- Use a backing strip for full penetration welds on thick materials.
- Clean the workpiece thoroughly to avoid contamination.
- Common Challenges and Solutions:
- Porosity: Ensure dry flux and clean base metal.
- Incomplete Fusion: Adjust voltage, amperage, or travel speed.
- Flux Entrapment: Use proper flux depth and welding parameters.
- Weld Cracking: Preheat material and control cooling rates.
- Safety Considerations:
- Wear appropriate PPE (helmet, gloves, flame-resistant clothing).
- Ensure proper ventilation to avoid inhaling fumes.
- Keep flux dry to prevent moisture-related defects.
- Be cautious of hot slag and spatter during and after welding.
- Follow electrical safety protocols to avoid shocks.
FAQ Content: Submerged Arc Welding (SAW)
1. What is Submerged Arc Welding (SAW)?
Direct Response: Submerged Arc Welding (SAW) is an automated or semi-automated welding process that uses a consumable electrode and a granular flux to create high-quality welds, primarily for thick materials and long, continuous joints.
Detailed Explanation: SAW involves forming an arc between a continuously fed wire electrode and the workpiece. The arc is “submerged” under a layer of flux, which shields the weld pool from atmospheric contamination, prevents spatter, and stabilizes the arc. This process is known for its high deposition rates, deep penetration, and efficiency in industrial applications.
Example: SAW is commonly used in shipbuilding to weld thick steel plates for hulls, ensuring strong, defect-free joints.
Additional Resources: American Welding Society (AWS) Guide to SAW
2. What materials can be welded using SAW?
Direct Response: SAW is primarily used for welding low-carbon steels, low-alloy steels, and stainless steels. It can also be used for some nickel-based alloys.
Detailed Explanation: SAW is ideal for thick materials (typically 5mm to 50mm or more) due to its deep penetration capabilities. It is not suitable for non-ferrous metals like aluminum or copper, as the flux composition and process characteristics are optimized for ferrous materials.
Example: In pipeline construction, SAW is used to weld high-strength, low-alloy steel pipes, ensuring durability and leak-proof joints.
Additional Resources: Material Compatibility Chart for SAW
3. What are the advantages of SAW over other welding processes?
Direct Response: SAW offers high deposition rates, deep penetration, minimal spatter, and excellent weld quality, making it ideal for heavy fabrication and thick materials.
Detailed Explanation: Compared to processes like MIG or stick welding, SAW is faster and more efficient for long, continuous welds. The flux layer eliminates the need for external shielding gas, reduces UV radiation, and produces clean, smooth welds with minimal post-weld cleanup.
Example: In manufacturing pressure vessels, SAW ensures consistent, high-quality welds that meet strict industry standards.
4. What are the common challenges in SAW and how can they be addressed?
Direct Response: Common challenges include porosity, incomplete fusion, flux entrapment, and weld cracking. These can be mitigated by proper setup, parameter adjustment, and material preparation.
Detailed Explanation:
- Porosity: Caused by moisture in the flux or contamination on the base metal. Use dry flux and clean the workpiece thoroughly.
- Incomplete Fusion: Adjust voltage, amperage, or travel speed to ensure proper heat input.
- Flux Entrapment: Maintain the correct flux depth and ensure proper alignment of the welding head.
- Weld Cracking: Preheat the material and control cooling rates to reduce thermal stress.
Example: In bridge construction, preheating steel components before welding prevents cracking in cold weather conditions.
5. What safety precautions should be taken during SAW?
Direct Response: Wear appropriate PPE, ensure proper ventilation, keep flux dry, and follow electrical safety protocols.
Detailed Explanation:
- PPE: Use a welding helmet, gloves, and flame-resistant clothing to protect against UV radiation, heat, and spatter.
- Ventilation: Ensure adequate airflow to avoid inhaling fumes generated during welding.
- Flux Handling: Store flux in a dry environment to prevent moisture absorption, which can cause defects.
- Electrical Safety: Inspect equipment for damaged cables and ensure proper grounding to avoid electrical hazards.
Example: In industrial settings, welding booths with exhaust systems are used to maintain air quality during SAW operations.
Additional Resources: OSHA Welding Safety Guidelines
6. Can SAW be used for outdoor welding?
Direct Response: SAW is generally not recommended for outdoor welding due to the risk of flux contamination from wind and moisture.
Detailed Explanation: The granular flux used in SAW can be blown away by wind or absorb moisture from the environment, leading to weld defects like porosity. SAW is best suited for controlled indoor environments where these factors can be managed.
Example: In pipeline construction, temporary shelters are often used to protect SAW operations from environmental conditions.
Additional Resources: Best Practices for SAW in Controlled Environments
7. What equipment is needed for SAW?
Direct Response: Key equipment includes a SAW power source, wire feeder, welding head, flux hopper, and workpiece fixtures.
Detailed Explanation:
- Power Source: Provides the necessary current (constant voltage or constant current).
- Wire Feeder: Continuously feeds the electrode wire.
- Welding Head: Holds the electrode and directs the flux.
- Flux Hopper: Stores and dispenses the granular flux.
- Fixtures: Secure the workpiece in place for consistent welding.
Example: In manufacturing, automated SAW systems are integrated with robotic arms for precision and efficiency.
Additional Resources: SAW Equipment Buying Guide