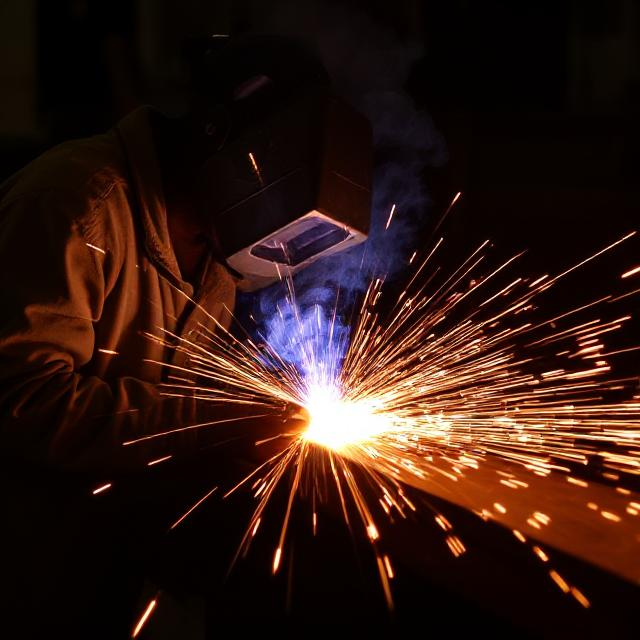
- 1. Name of Process:
Thermite Welding
2. Key Features:
- Uses an exothermic reaction to generate heat (up to 2500°C).
- No external power source required.
- Ideal for joining large sections of metal.
- Produces strong, durable welds.
- Commonly used for rail welding and heavy repairs.
3. Applications:
- Railway track welding.
- Joining heavy steel structures (e.g., pipelines, shipbuilding).
- Repairing cracks in large metal components.
- Electrical grounding connections.
4. Recommended Tools and Equipment:
- Thermite mixture (aluminum powder and metal oxide).
- Crucible and mold (customized for the workpiece).
- Ignition source (sparkler or magnesium ribbon).
- Preheating torch (for large workpieces).
- Safety gear (gloves, goggles, fire-resistant clothing).
5. Setup and Settings:
- Clean and align the joint area thoroughly.
- Secure the mold around the joint.
- Preheat the workpiece if necessary (especially for large sections).
- Pour the thermite mixture into the crucible and ignite.
6. Technique Tips:
- Ensure proper alignment of the mold to avoid leaks.
- Use the correct thermite mixture for the material being welded.
- Preheat the workpiece to avoid incomplete fusion.
- Allow sufficient cooling time before removing the mold.
7. Common Challenges and Solutions:
- Incomplete Fusion: Preheat the workpiece adequately.
- Leaks in Mold: Ensure the mold is tightly sealed and properly aligned.
- Slag Inclusion: Use high-quality thermite mixture and clean the joint area thoroughly.
- Excessive Heat Loss: Work in a controlled environment to minimize heat dissipation.
8. Safety Considerations:
- Wear fire-resistant clothing, gloves, and safety goggles.
- Work in a well-ventilated area to avoid fume inhalation.
- Keep a fire extinguisher nearby.
- Avoid contact with molten metal and hot surfaces.
- Follow manufacturer guidelines for handling thermite mixtures.
FAQ Thermite Welding:
1. What is Thermite Welding?
Thermite welding is a process that uses an exothermic reaction between aluminum powder and metal oxide to generate intense heat, melting metal to form a weld.
The reaction produces temperatures up to 2500°C, which melts the metal oxide (usually iron oxide) and forms molten metal. This molten metal is poured into a mold around the joint, creating a strong, durable weld without the need for external power.
Examples or Case Studies:
- Widely used for welding railway tracks, ensuring seamless and robust joints.
- Applied in repairing large steel structures, such as ship hulls or pipelines.
Additional Resources:
- Thermite Welding Basics – American Welding Society (AWS)
- Thermite Welding Applications – ScienceDirect
2. What materials can be welded using thermite welding?
Thermite welding is primarily used for steel, cast iron, and other ferrous metals.
The process is ideal for materials that require high-strength welds, such as railway tracks, heavy steel structures, and large pipes. It is less commonly used for non-ferrous metals due to the specific chemical reactions involved.
Examples or Case Studies:
- Railway tracks made of high-carbon steel are commonly welded using thermite.
- Large steel beams in construction projects are joined using thermite welding for durability.
Additional Resources:
3. What are the advantages of thermite welding?
Thermite welding offers portability, high-strength welds, and the ability to join large sections without external power.
The process is highly portable, making it ideal for field repairs and remote locations. It produces strong, durable welds with minimal equipment, and it can weld large sections of metal in a single operation.
Examples or Case Studies:
- Railway maintenance crews use thermite welding for on-site track repairs.
- Thermite welding is used in remote pipeline construction where power sources are unavailable.
Additional Resources:
4. What are the limitations of thermite welding?
Thermite welding is limited by its high heat output, lack of precision, and suitability primarily for ferrous metals.
The intense heat can cause distortion in thin or delicate materials. The process is also less precise compared to other welding methods and is not suitable for non-ferrous metals or small components.
Examples or Case Studies:
- Thin steel plates may warp due to the high heat of thermite welding.
- Non-ferrous metals like aluminum cannot be welded using standard thermite mixtures.
Additional Resources:
5. What safety precautions are necessary for thermite welding?
Safety precautions include wearing fire-resistant clothing, gloves, goggles, and working in a well-ventilated area.
The process generates extreme heat and molten metal, which can cause severe burns or fires. Proper protective gear and a controlled environment are essential to prevent accidents.
Examples or Case Studies:
- Industrial workers use fire-resistant aprons and face shields during thermite welding.
- Fire extinguishers and sand buckets are kept nearby to handle spills or fires.
Additional Resources:
6. How do I set up for thermite welding?
Set up involves cleaning the joint, aligning the mold, preheating the workpiece (if necessary), and igniting the thermite mixture.
The joint area must be clean and properly aligned to ensure a strong weld. The mold is secured around the joint, and the thermite mixture is ignited in a crucible. The molten metal is then poured into the mold to form the weld.
Examples or Case Studies:
- Railway workers use preheating torches to warm the track before pouring the thermite mixture.
- Custom molds are designed for specific joints, such as pipeline connections.
Additional Resources:
7. What are common challenges in thermite welding and how are they resolved?
Common challenges include incomplete fusion, slag inclusion, and excessive heat loss, which can be resolved through proper setup and technique.
- Incomplete Fusion: Preheat the workpiece to ensure proper melting.
- Slag Inclusion: Use high-quality thermite mixture and clean the joint thoroughly.
- Excessive Heat Loss: Work in a controlled environment and use insulating materials.
Examples or Case Studies:
- In railway welding, preheating ensures complete fusion of the track joints.
- Slag inclusions are minimized by using premium thermite mixtures and clean workpieces.
Additional Resources: